Multi-Sensor
Pipe Inspection
Multi-Sensor Robotic Condition Assessment
SewerVUE Technology is uniquely equipped with the latest msi technologies to tackle a wide variety of condition assessment projects. Our versatile multi-sensor inspection (MSI) system can collect quantitative data from non-ferrous pipes of all shapes and sizes. Using a combination of LiDAR, sonar, CCTV, and SewerVUE proprietary pipe penetrating radar technology, SewerVUE is equipped with all the tools to get the job done.

PPR
Pipe penetrating radar, or PPR, is SewerVUE’s proprietary condition assessment method. By utilizing GPR technology from the inside of a pipe, PPR can see past the pipe wall and reveal what lies beyond; wall thickness, rebar cover, and voids can all be seen with a PPR inspection.
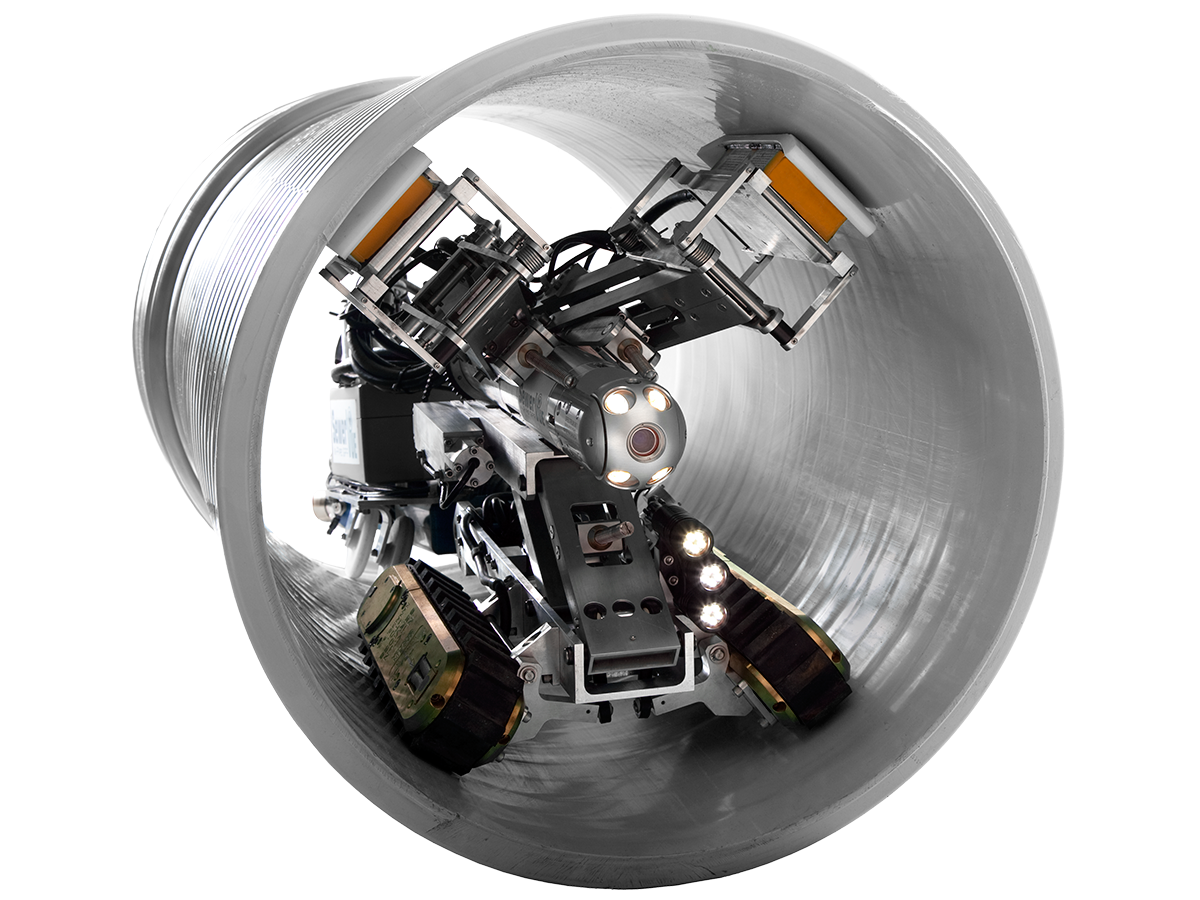
Learn more here.
Sonar
Sonar is the use of sound propagation to create an image of the pipe’s inner surface below the flow line. SewerVUE’s sonar technology details the pipe's profile and measures sediment volume, all with sub-centimetre accuracy. A sonar pipe inspection in conjunction with LiDAR imaging enables SewerVUE to generate a 360-degree image of the pipe that includes quantitative determination of ovality, wall loss, sediment volume, and depth, even through tight bends.
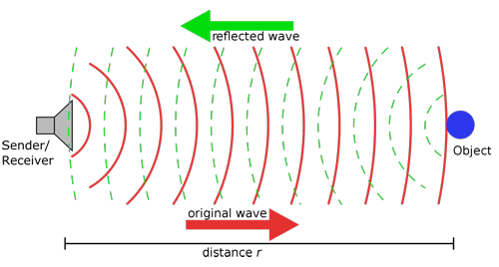
LiDAR
Light and Radar, or LiDAR, is a multi-sensor (MSI) inspection method among pipes. LiDAR surveys are done by projecting a laser, and measuring the time it takes for it to reach a target and reflect back to the sensor. A LiDAR survey collects continuous 2-D cross sections of the pipe wall. By compiling these cross sections, a high-resolution 3-D model is created. SewerVUE offers advanced MSI inspections utilizing LiDAR imaging to deliver sub-centimetre accuracy. LiDAR is used to measure the pipe above the flow line. It collects highly detailed information about ovality, deformations, offset joints, and lateral size.
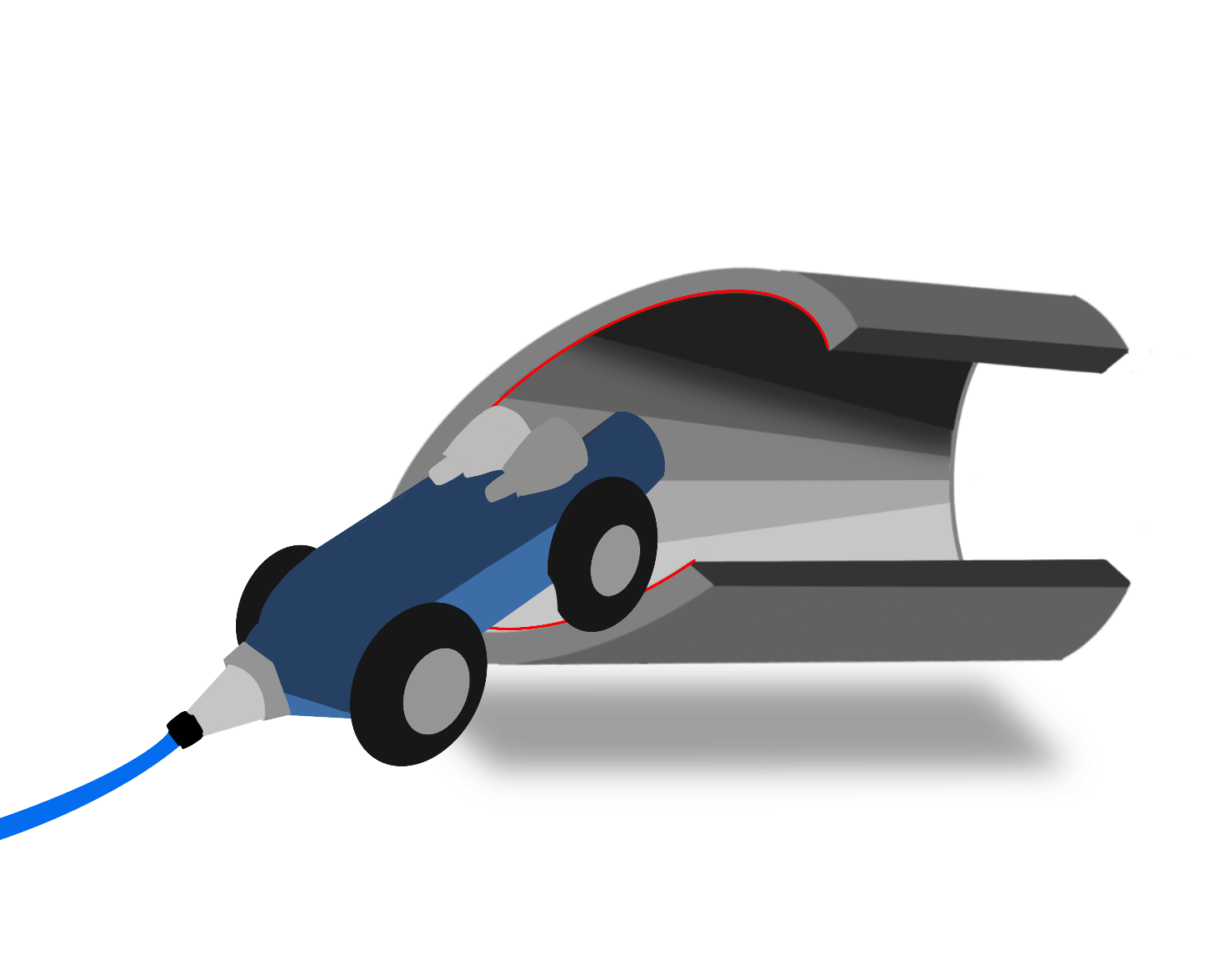
CCTV
CCTV is the most well-known condition assessment method, and is included in all of our surveying operations. A CCTV feed is used to navigate our ROVs past unexpected obstacles in pipes, but is also useful in identifying any visual anomalies discovered by the other, more advanced inspection techniques.
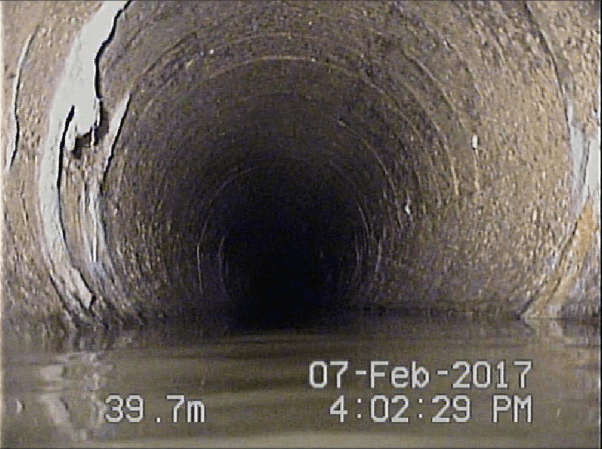
4-in-1 Viewer
With so much information available through SewerVUE’s MSI technologies, organizing the data in a useful manner is crucial. SewerVUE uses advanced proprietary software to visualize the data. PPR, LiDAR, sonar, and CCTV results are delivered in a comprehensive post-inspection report. The information is also viewable in SewerVUE’s 4-in-1 software. The 4-in-1 Viewer allows for all of the information collected from a survey to be viewed simultaneously, with an intuitive layout.
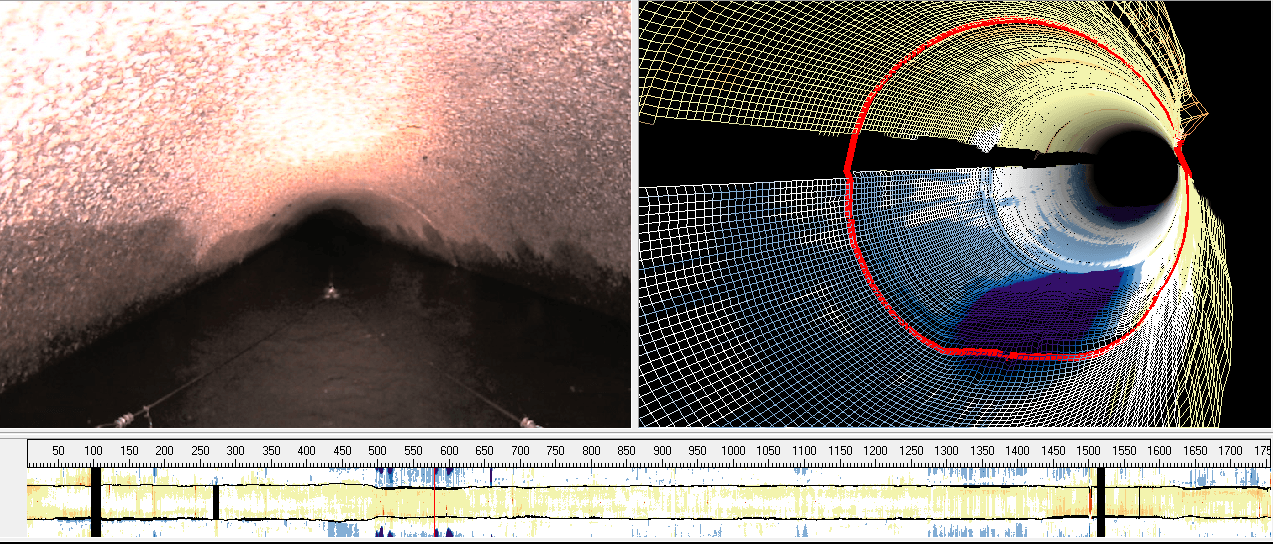
In a world of tight budgets, an effective asset management plan is essential.
SewerVUE Technology’s inspection methods provide the quantitative data needed to design such a plan, and they do so in a safe, fast, and cost-effective way.
Contact us today to see how SewerVUE's MSI technology can meet your needs.